In our previous discussion, we explored issues with the wire feeder of handheld laser welding machines. Today, we’ll focus on another common issue: safety lock alarms. This is an important feature designed to enhance operational safety, but when triggered incorrectly, it can disrupt your welding process. In this article, we’ll explain the potential causes of safety lock alarms and provide step-by-step solutions to help you address the problem effectively.
Understanding the Safety Lock Alarm
The safety lock alarm is a safeguard mechanism in handheld laser welding machines, preventing accidental operation. When triggered, it stops the machine from functioning until the issue is resolved. Typically, the alarm is activated when the welding gun and ground clamp do not form a complete circuit or when there are electrical connection issues.
Common Causes of the Safety Lock Alarm
- The Welding Gun and Ground Clamp Do Not Form a Circuit
- If the gun tip and ground clamp are not properly connected to create a closed circuit, the safety lock alarm will be activated.
- Disconnected or Faulty Wiring
- The safety lock alarm can also be triggered by:
- A broken ground clamp wire.
- A damaged safety lock “+” wire from the gun tip.
- Loose or faulty wiring connections.
- The safety lock alarm can also be triggered by:
- Damaged Terminals or Control Box Port
- The safety lock terminal on the control box or the connection terminal itself may be damaged, preventing proper signal transmission.
Solutions to Address the Safety Lock Alarm
1. Ensure the Welding Gun and Ground Clamp Form a Circuit
- Why: The safety lock alarm is a protective feature that activates when the circuit between the gun and the ground clamp is incomplete.
- Solution:
- Check that the welding gun tip and the ground clamp are properly connected to form a closed circuit.
- Once the circuit is established, the safety lock alarm will automatically deactivate.

2. Check for Wiring Issues with a Multimeter
- Why: Wiring faults, such as broken connections or poor contact, can trigger the safety lock alarm.
- Solution:
- Inspect the Ground Clamp Wire:
- Set a multimeter to the continuity mode.
- Place one probe on the ground clamp and the other on the wire connected to the control box terminal (CN6, please check the pictures below).
- If the circuit is complete, the multimeter will beep, indicating continuity.
- If there’s no continuity, the wire is broken and needs to be repaired or replaced.
- Inspect the Ground Clamp Wire:
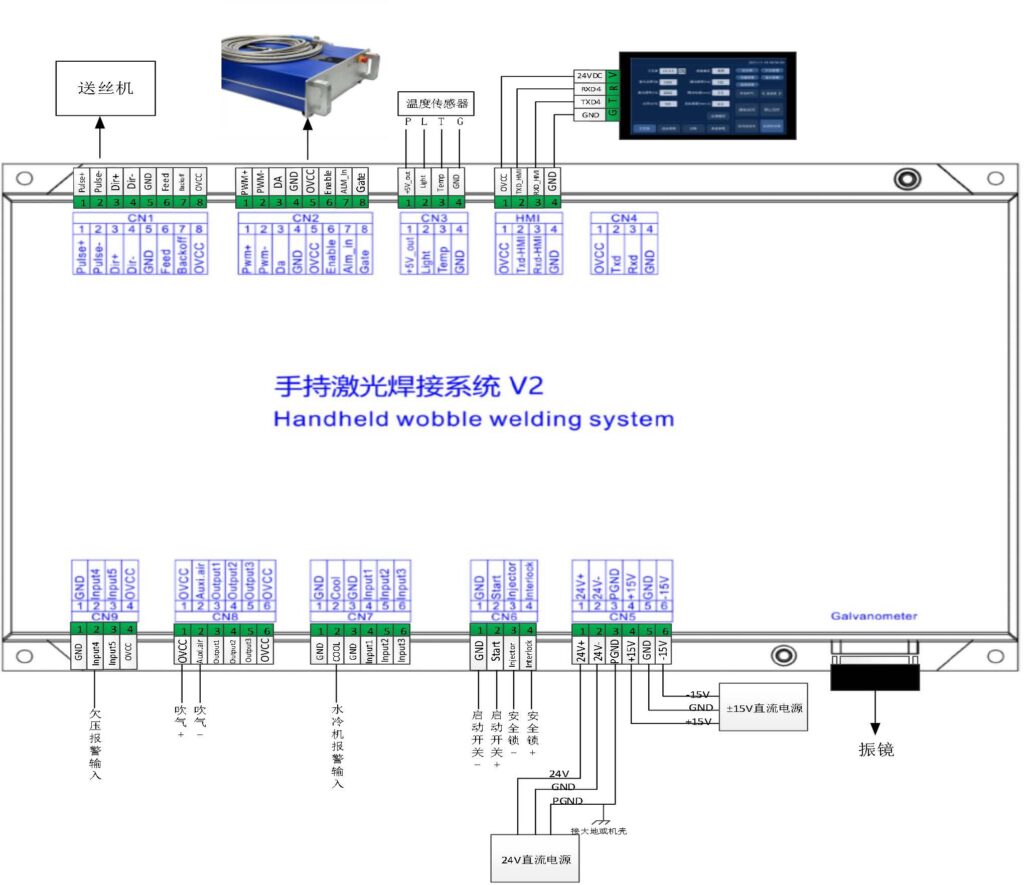
- Inspect the Safety Lock “+” Wire on the Gun:
- Use the multimeter to test the continuity of the safety lock “+” wire.
- Place one probe on the set screw of the gun’s protective lens and the other on the CN6 safety lock “+” wire terminal in the control box.
- If there’s no continuity, inspect the wire for damage and replace it as necessary.
3. Test the Control Box Ports and Terminals
- Why: Faulty ports or damaged terminals in the control box can also prevent the safety lock mechanism from functioning properly.
- Solution:
- Use a jumper wire to short-circuit pins 3-4 of the CN6 terminal in the control box.
- If the alarm disappears, it indicates that both the terminal and the port are functioning correctly.
- If the alarm persists:
- Replace the connection terminal and short-circuit pins 3-4 again.
- If the problem remains, the control box port itself is damaged and needs to be replaced.
Preventive Maintenance Tips
- Regularly Inspect Connections:
- Periodically check all wires, clamps, and terminals for signs of wear or damage to prevent sudden malfunctions during operation.
- Protect the Control Box:
- Keep the control box in a dry, clean environment to avoid damage to sensitive components.
- Follow Manufacturer Guidelines:
- Always adhere to the machine’s user manual for proper operation and maintenance procedures.
Conclusion of laser welder safety lock alarm troubleshooting.
The safety lock alarm in handheld laser welding machines is an essential safety feature designed to prevent accidental operation. However, if triggered incorrectly, it can interrupt your work. By understanding the causes—such as incomplete circuits, faulty wiring, or damaged control box components—you can troubleshoot and resolve the issue efficiently.
With the solutions provided in this guide, you can ensure safe and seamless welding operations while maintaining the reliability of your equipment. If you encounter persistent problems, consult the machine’s manufacturer or seek professional technical assistance.
Safety is key—understanding and resolving safety lock alarms will help keep your welding processes smooth and secure.
If you need further supports, please contact our team now.